Alumina is an important ingredient in ceramics, as it has many useful properties. These qualities include high wear resistance, refractory properties, and electrical insulating properties. However, its importance in ceramics goes beyond these properties. To better understand the material, let’s look at its uses.
High wear resistance
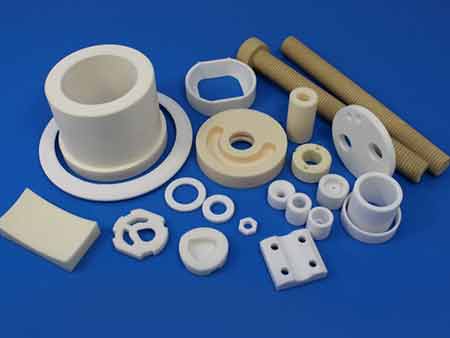
High wear resistance is an important property of alumina ceramic This is because alumina is hard and is resistant to abrasion. Because of its hardness, alumina is also resistant to high temperatures and acids. As a result, alumina is highly resistant to the effects of chemicals and does not corrode.
Alumina ceramics are 99% alumina and have excellent wear resistance. To improve wear resistance, the Al2O3-Gd2O3-CaO-MgO system was studied. Its Gd2O3 content was varied from 0.01% to 1%. The materials were then subjected to ball milling in water. The effects of Gd2O3 were evaluated, as were bulk density, grain growth mode, and grain boundary cohesion.
Refractory properties
The refractory properties of alumina in ceramic materials are largely dependent on the underlying mineral composition. Among the minerals with high refractory potential are alumina, spinel, mullite, corundum, and periclase. The properties of these minerals are dependent on their composition and texture, and are therefore reflected in their physical properties.
Refractory ceramics are used for high-temperature processing applications. These materials are typically alumina or magnesia-based but can be made from other compositions as well. While most refractory ceramic structures are high-density, some contain porous components that are useful for insulation or filtration. This article describes the properties of these materials and explores the relationships between process conditions, composition, and structure.
Machinability
Alumina is a highly machinable material, with a high degree of compressive strength. Its compressive strength is two to five times that of tool steel, which makes it a highly desirable material for structural applications. Another characteristic of alumina is its resistance to bending and distortion under load. This property makes alumina ideal for structural applications where bending and deformation of metals and plastics are a major source of failure.
Alumina ceramics are very popular in advanced manufacturing applications due to their excellent properties. Research has focused on evaluating the influence of process variables such as spindle speed, feed rate, coolant pressure, and tool position on alumina ceramic machining. The research employed response surface methodology to examine the effects of these parameters on the machining process. The experimental setup consisted of a central composite rotatable design. In addition, variance analysis was performed to determine the effects of each process parameter. Afterwards, the microstructure of the machined rod samples was analyzed with a scanning electron microscope.
Electrical insulator
Alumina is an electrical insulator that is used in many industrial applications. Its high hardness and low erosion levels make it a versatile material with multiple uses. Its temperature resistance, corrosion resistance, and bio-inertness make it ideal for use in high-temperature applications. Precision Ceramics produces a wide variety of alumina ceramic tubes and insulators for many technical applications.
Summary:
Alumina ceramics are frequently used in vacuum electrical devices. Their excellent electrical insulating properties make them a valuable choice for these applications. However, due to their chemical stability, they can be difficult to braze with metal directly. To overcome this difficulty, alumina ceramic surfaces are first metallized using the Mo-Mn method. The resulting metal-alumina joint is then brazed onto the alumina surface. The process is difficult because negative high voltages can cause surface flashover.